The global pet food market is expected to expand at a CAGR of approximately 8.5% over the next five years, driven by the increasing number of pet owners and the evolving trend of placing greater emphasis on pet health and food nutrition. It is every manufacturer's dream to be part of a growing industry, but capital expenditures are limited, the sector's workforce is dwindling, and production facilities lack aging equipment and manual labor that threaten productivity. As there are many processes involved, growth comes with its own challenges.
Meeting increasing demands with limited resources requires maximizing the potential of current equipment and processes. But how? Simply put, it's automation. How to incorporate the right combination of automation tools, such as in-line robotics, advanced vision systems, and cutting-edge artificial intelligence (AI) algorithms, to enhance current assets and processes and help plants meet next challenges. Let's see if we can prepare for it. Future tasks.
RoboRescue: Closing the labor gap
With many skilled workers retiring and Gen Z showing little desire to complete the hot, hard, and dangerous jobs often found on factory floors, they may find it difficult to meet the immediate increase in demand. there is. Rather than competing fiercely with other manufacturers for limited labor or wasting time recruiting and training workers who quickly realize they are not suited for the job, Let's work on it forever. It's time to welcome steel collar workers.
By bringing the power of robots to the floor, we can permanently fill open positions. Automate routine, repetitive, and dangerous tasks. Free up valuable human resources to focus on more important tasks. And it eliminates many of the inefficiencies that prevent you from reaching peak production.
Incorporate next-level quality measures
Pets are part of the family, and owners want to ensure that they receive the safest and most nutritious diet possible. As a pet food processor, ensuring product safety is a big responsibility. Strict food safety regulations in many places are consistent with human food safety standards. Especially since pet food is often too tempting for children.
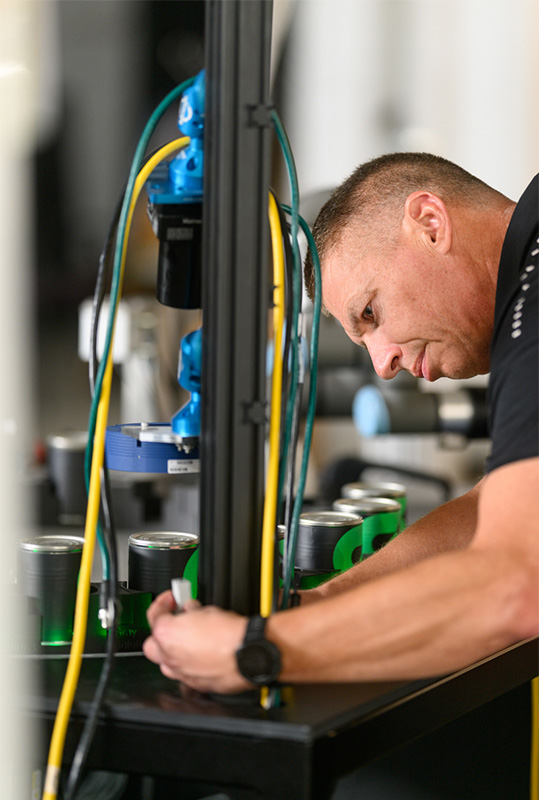
Source: ©Gray Solutions
“When processes like ingredient tracking and recipe management are performed manually, it's very easy to make mistakes,” says Diaz McDaniel, senior manager of process engineering at Gray Solutions. “Instead of running papers around the factory or digging deep into spreadsheets to ensure recipes are followed accurately and products are closely tracked throughout the production process, we add a software-based tracking system to existing equipment. can.”
With this digital toolset in place, everything is automatically tracked, from the ingredients that go into food to the exact location where pallets of product are delivered. This end-to-end transparency helps improve regulatory compliance and, in the unfortunate event of a recall, significantly narrows the scope to a specific batch, reducing both physical and social risks. Limit.
Another automated quality improvement tool to consider is the addition of a clean-in-place (CIP) system. CIP automates the cleaning of equipment between runs of different food blends, reducing changeover time and ensuring much more thorough cleaning than human capabilities. For example, you can use hotter water if you don't have to worry about human burns. hand. CIP also helps avoid issues such as cross-contamination, which can be harmful when food blends need to be processed to ensure that certain allergens are not present.
Quality can also be significantly improved by using vision-based inspection systems integrated throughout the production process to overcome many of the limitations of the human eye, from reading speed to the visible color spectrum. Vision systems perform many daily tasks, from inspecting incoming raw materials to checking for cracks and contaminants in the containers food is packaged in, to making sure products are perfectly packaged and palletized before shipping. Automate and significantly accelerate inspection-based quality tasks.
Let Curiosity Lead – Gray Solutions from Gray Solutions on Vimeo.
“The speed with which many of these tasks can be accomplished is amazing,” says Adam Richards, food safety engineer at Gray Solutions. “Throughput increases as the vision system inspects more than 1,200 cans per minute for proper serialization, and the vision system detects moisture levels within grain bags to prevent problems such as mold. Imagine the quality improvement you experience when you prevent growth.”
Additionally, if the vision system is connected to a process controller, defective products can be automatically rejected and alarms can alert operators to potential major problems. If problems are identified early, they can be corrected long before defective or contaminated products reach consumers.
Technological tailwind: Adding advanced automation tools
If you're starting to introduce automation to your production line using these robots and vision-based tools, but are still looking for ways to get more out of your existing processes and equipment, consider additional advanced automation tools is needed.
Advanced robots, such as Spot® from Boston Dynamics, can take many of the measures already discussed to a new level. Spot can supplement the workforce by performing routine tasks such as routine retrieval missions to remove bags of material for in-lab quality analysis. Improve uptime by scanning and spot patrolling your factory floor before potential maintenance issues occur.
In addition to robotic tools such as Spot, autonomous mobile robots (AMRs) can be used to improve logistics within your facility. Taking on the difficult task of transferring large quantities of raw materials or his 50-pound bags of finished dog food from human hands to his AMR arms greatly increases the speed and accuracy of material handling. Additionally, AMR is highly flexible and can be easily modified to adapt to dynamic production environments.
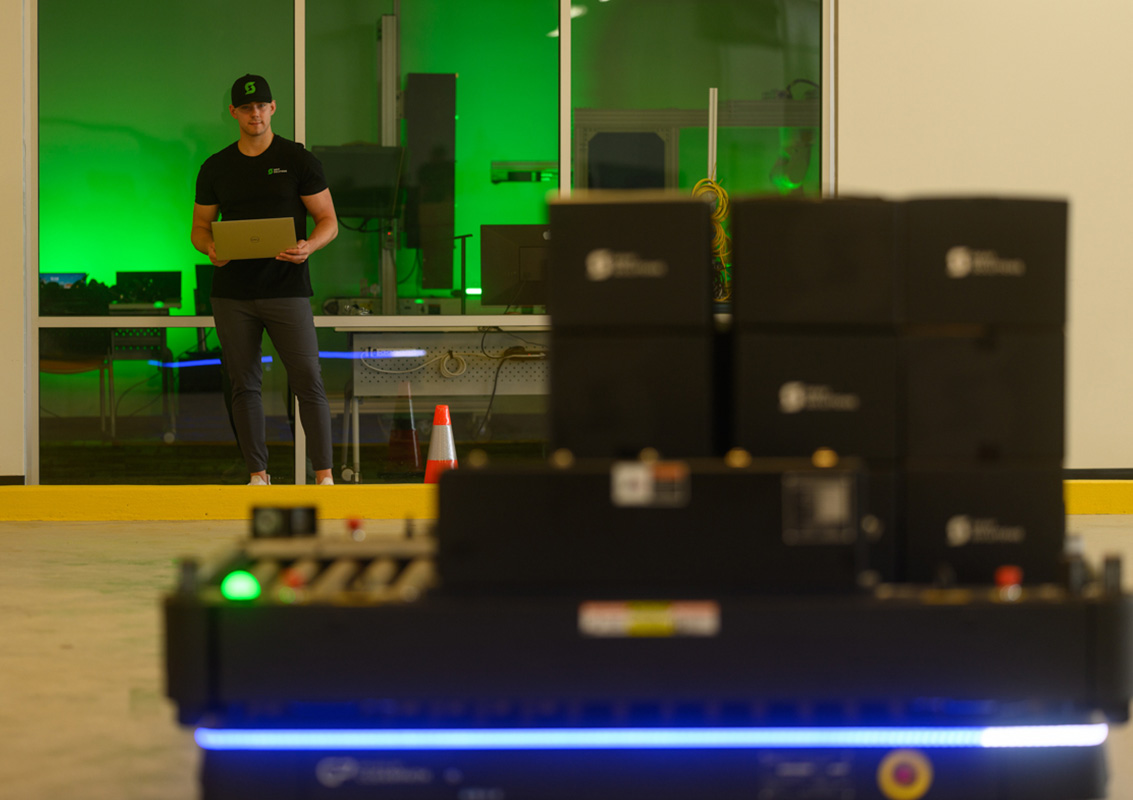
Source: ©Gray Solutions
Finally, we must mention the huge potential for AI to revolutionize many areas of the pet food production process. Machine learning algorithms can extract trends from data, allowing you to fine-tune processes for maximum efficiency or perform preventive maintenance before problems occur to reduce emergency downtime. Advanced AI-based vision tools can improve quality standards, for example by allowing hyperspectral cameras to see differences in color that the human eye would never detect, and by looking for incredibly subtle differences. and guarantees optimal flavor.
Embrace the transformative power of automation
With the demand for pet food on the rise and pet owners increasingly concerned about the quality of their pet food, now is the time to examine your current pet food production process and introduce automation to eliminate inefficiencies. This is a great time to identify opportunities. But evaluating the many automation options available can be overwhelming. So let's discuss. We can work with you to create a plan that redefines what is possible in your production by bringing robotics to the factory floor and enhancing quality measures with advanced vision-based inspection systems. .
Want to learn more? Check out the Pet Food Processing article starting on page 24 in the March issue to learn how Gray Solutions brought state-of-the-art automation and Make sure you have incorporated robotics tools. www.graysolutions.com.